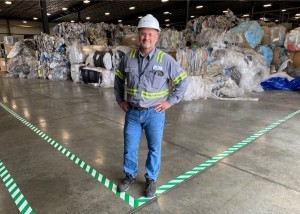
The president of plastics at Brightmark stands amid 900 tons of waste plastic in Indiana. Their purpose is to turn plastic waste into diesel fuel, naphtha and wax.
From an Article by James Bruggers, Inside Climate News, September 11, 2022
ASHLEY, Indiana—The bales, bundles and bins of plastic waste are stacked 10 feet high in a shiny new warehouse that rises from a grassy field near a town known for its bright yellow smiley-face water tower.
Jay Schabel exudes the same happy optimism. He’s president of the plastics division of Brightmark Energy, a San Francisco-based company vying to be on the leading edge of a yet-to-be-proven new industry—chemical recycling of plastic.
Walking in the warehouse among 900 tons of a mix of crushed plastic waste in late July, Schabel talked about how he has worked 14 years to get to this point: Bringing experimental technology to the precipice of what he anticipates will be a global, commercial success. He hopes it will also take a bite out of the plastic waste that’s choking the planet.
“When I saw the technology, I said this is the sort of thing I can get out of bed and work on to change the world,” said Schabel, an electrical engineer. “My job is to set it up and get it running,” he said of the $260 million, 120,000 square foot building and adjacent chemical operations. “Then perpetuate it around the world.”
But the company, which broke ground in Ashley in 2019, has struggled to get the plant operating on a commercial basis, where as many as 80 employees would process 100,000 tons of plastic waste each year in a round-the-clock operation.
Schabel said that was to change in August, with its first planned commercial shipment of fuel to its main customer, global energy giant BP. But a company spokesman said in mid-August that the date for the first commercial shipment had been pushed back to September, with “full-scale operation…extending through the end of the year and into 2023.”
Even with that new timetable, the plant, located along Interstate 69 in the northeast corner of Indiana, Brightmark faces ongoing economic, political and — environmental critics and some scientists say — technical headwinds. Its business model must contend with plastics that were never designed to be recycled. U.S. recycling policies are dysfunctional, and most plastics end up in landfills and incinerators, or on streets and waterways as litter.
Environmental organizations with their powerful allies in Congress are fighting against chemical recycling and the technology found in this plant, known as pyrolysis, in particular, because they see it as the perpetuation of climate-damaging fossil fuels. “The problem with pyrolysis is we should not be producing more fossil fuels,” said Judith Enck, a former regional director of the U.S. Environmental Protection Agency and the founder and executive director of Beyond Plastics, an environmental group. “We need to be going in the opposite direction. Using plastic waste as a feedstock for fossil fuels is doubling the damage to the environment because there are very negative environmental impacts from the production, disposal and use of plastics.”
The global plastics crisis is well documented with annual plastic production soaring from 20 million metric tons to 400 million metric tons over the last five decades. Nearly all are made from fossil fuels and much is designed to resist biodegradation and can last in the environment for hundreds of years, increasingly as microscopic bits that are ubiquitous and have invaded the human body.
The amount of plastic discharged into the ocean could reach up to 53 million metric tons per year by 2030, or roughly half of the total weight of fish caught from the ocean annually, according to a December report by a committee of scientists with the National Academies of Sciences, Engineering and Medicine.
The U.S. produces the most plastic waste in the world, nearly 300 pounds per person in a year, the report found. But only a small percentage, less than 6 percent, of plastics used by consumers in the U.S. actually get recycled, a recent analysis of EPA data by Beyond Plastics and the Last Beach Cleanup found.
What does get recycled, such as soda bottles, typically goes through a mechanical process involving sorting, grinding, cleaning, melting and remolding, often into other products. But there are limits to the kinds of plastics that are acceptable for mechanical recycling and how many times these plastics can be re-used in this way.
Chemical recycling, called advanced recycling by the chemical industry— which touts it as almost a Holy Grail of solutions—seeks to turn the harder-to-recycle kinds of plastic waste back into plastics’ basic chemical building blocks. Pyrolysis is among the chemical recycling technologies getting the most attention, with industry representatives saying pyrolysis can turn mixtures of plastic waste into new plastic, fuel or chemicals for making everything from detergents to cars to clothing.
With these plastic wastes, such as grocery bags, cups, lids, containers and films, the industry claims, pyrolysis heats them at high temperatures in a vessel, with little or no oxygen and sometimes with a chemical catalyst, to create synthetic gases, a synthetic fuel called pyrolysis oil, and a carbon char waste product. It’s a process that’s been around for centuries, used for making tar from timber for wooden ships in the 1600s, for example, or coke from coal for steelmaking in the last century.
Brightmark describes its plant as the “largest-scale pyrolysis facility in the world.” It is designed to take plastic waste hauled in from municipal and industrial sources. The waste is cleaned, chopped up and pressed into small pellets, then fed into pyrolysis tanks and heated by burning natural gas. The synthetic gas created by the pyrolysis process is then mixed with the natural gas to generate temperatures between 800 degrees and 1,500 degrees Fahrenheit, Schabel said.
“We flush the molecules out and condense them,” Schabel said, describing what the high heat does to the plastic waste. “We are hitting them with a thermal hammer to break them into pieces. They want to come back together but we control how they come back together.”
The char is sent to a landfill as non-hazardous waste, he said, and the pyrolysis oil goes to a small-scale refinery behind the warehouse, where it’s separated into low-sulfur diesel fuel, flammable liquid naphtha, and wax for industrial uses or candles. “We call this a hyper-local oil well,” Schabel said on the tour. But a lot of what comes into the plant gets lost in the process.
In a document Brightmark filed in December with the EPA, the company acknowledged that just 20 percent of the plant’s output is its primary product — what it described as fuels. Most of the rest, 70 percent, is the synthetic gas that the company said is combusted with natural gas to generate heat, with 20 percent of that syngas burned away in a flare. The rest is the char, according to the filing.
The company now disputes its own numbers, with a spokeswoman saying company officials are working to get them corrected to reflect a larger percentage of output as diesel fuel or naphtha. But the EPA filing plays into one of the sharpest criticisms of pyrolysis — that it’s not really plastics recycling at all.
With pyrolysis, “what you make is what I would call, and I grew up in New Jersey, so forgive me, a dog’s breakfast of compounds,” said University of Pittsburgh Professor Eric Beckman, a chemical engineer with a Ph.D. in polymer science. “It’s like everything you can think of, gases, liquids, solids,” he said.
If plastic waste could be turned only into naphtha, a bonafide building block for plastics, a company could operate what Beckman called a closed loop, and circular system for plastics that could be considered recycling, he said. But that is not what pyrolysis does.
“And this is where it gets controversial,” Beckman said, adding: “because you have people doing this who are saying, ‘We’re recycling it.’ No, you’re not. You’re burning it.” And any time that fossil fuels are being burned, he said, they are emitting greenhouse gas and air pollutants.
Jan Dell, a chemical engineer who has worked as a consultant to the oil and gas industry and now runs The Last Beach Cleanup, a nonprofit that fights plastic waste, agreed. “The fact that pyrolysis operations have to burn so much of the material to get to the high temperatures is a fundamental flaw,” she said.
>>> To be continued tomorrow …….
{ 1 comment… read it below or add one }
I am a American Blue collar worker..”Cost of living to wages today” Can I afford Diesel fuel? Can I help the enviroment by lowering greenhouse gas? When will we be in the Real 21st Century? My answer to all of this is..”I will use pyrolysis to make home made fuel to survive and help people in need. Mixing it with home made wood alcohol..also pyrolysis….